Modeling The Future With BIM
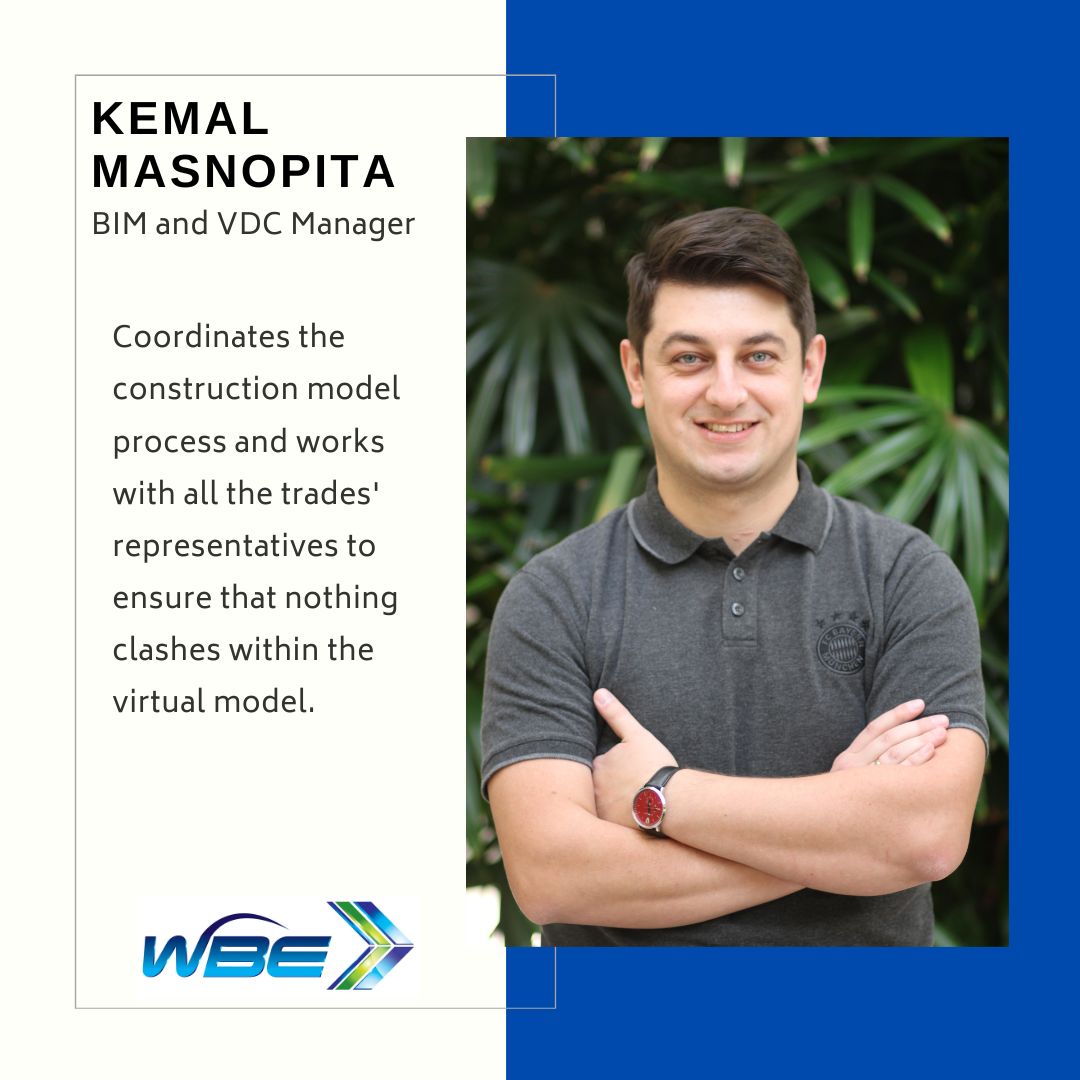
Remember when everything in the building industry was done by hand? When blueprints were genuinely blue, and we used hammers instead of nail guns? How often was there a chasm between the architect’s vision and the builder’s reality on the ground?
PDF construction documents have long since replaced blueprints with all the drawings, instructions and specs needed for each part of the build. And the design process improved markedly in the 1990s when Computer Assisted Design (CAD) arrived on the scene.
But construction design and planning technology has moved in leaps and bounds since then, and the development of BIM and VDC systems has revolutionized the possibilities for owners, architects and contractors.
Introducing BIM and VDC
Building Information Modeling (BIM) is a collaboration process or system using the latest digital technology that allows everyone on the project to work together on the same set of designs. VDC stands for Virtual Design and Construction. You can create detailed digital simulations of buildings and building sites using VDC technology, allowing everyone involved to identify and solve potential problems before they arise.
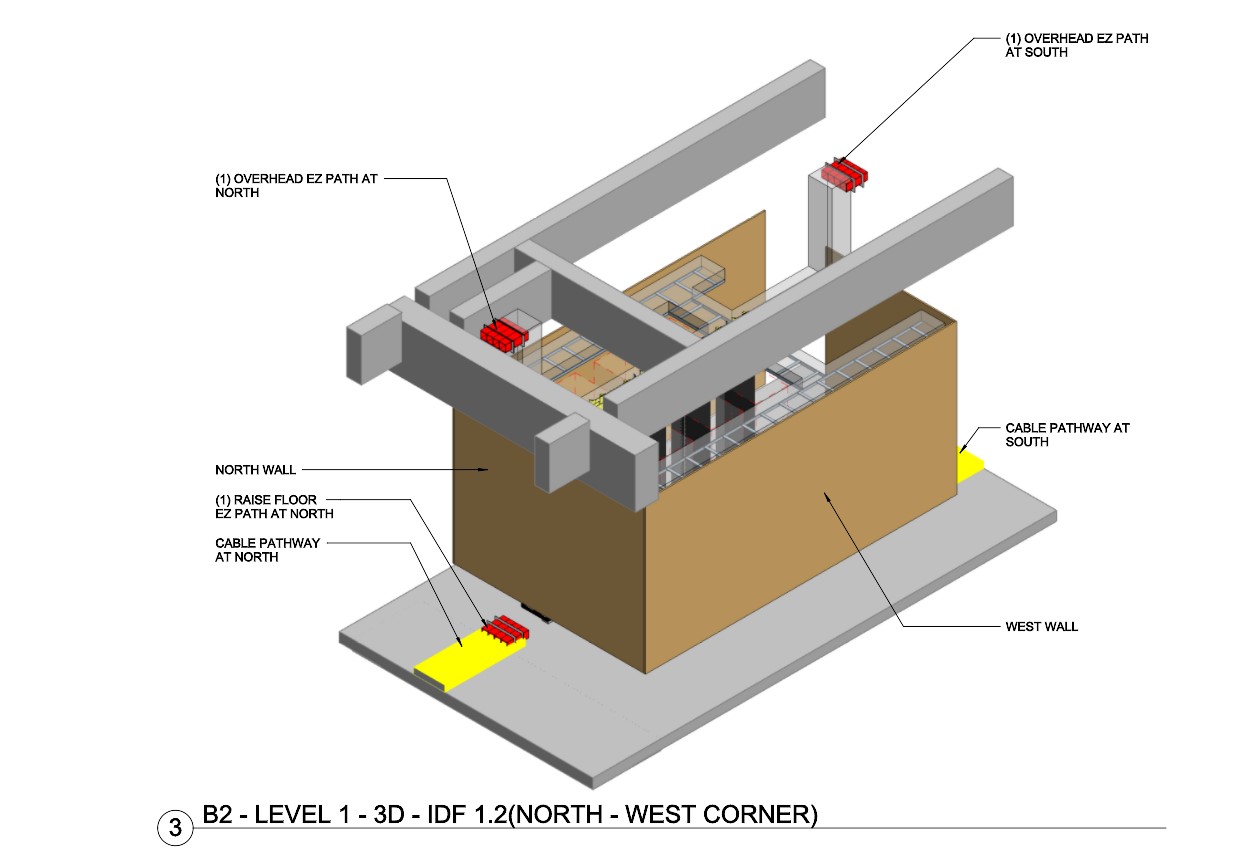
The Building Information Modeling Process
So, what does it look like when BIM enters the design mix?
First, the architect consults with the owner and contractors and draws up the building plans as a detailed 3D model. Next, the electrical engineer, plumber, and GC can add their input to the same digital files. They can work simultaneously or sequentially to produce an immensely detailed computer model and set of design documents.
From the design phase, the model goes to the pre-construction phase. The GC and sub-contractors can now work on the design requirements. For example, the electrical contractor looks at all the loads, where cables will go, what machinery will be installed, etc.
They can then decide on the actual hardware needed to fulfill all that. That allows them to calculate the exact conduit sizes, what mounting supports the cable tray will need and so on. At the same time, the plumber can layer in the drainage, water mains and sewerage pipes.
They’ll see where the bathrooms and kitchen facilities are and can calculate piping etc. The builders can see how much scaffolding they’ll need to use, calculate how many steel supports to order and how much insulation and lining they’ll need in each room.
BIM and VDC models include everything from fire alarms and security camera placement to the size of the screws and the design of the light fittings. Often it looks at the total package, including the car parking, landscaping, fencing and so on.
Imagine the potential for savings in money, time and materials that come from being able to see everything before the first sod is turned.
That’s why W. Bradley Electric recently appointed Kemal Masnopita as their first-ever BIM and VDC manager. This vertical presents an exciting new direction for WBE and gives our construction clients and contractors the confidence to use BIM and VDC technology now and into the future.
Introducing Kemal
Masnopita began his working life a long way from America and even further away from the construction industry. In fact, he completed a master’s in journalism and worked for several years as a TV journalist at home in Bosnia Herzegovina, a small country in Southeast Europe.
Then, in 2014, without knowing a word of English, Kemal moved to the United States and became fascinated with the possibilities of VDC technology. He joined a software company and simultaneously immersed in learning English and BIM modeling, while understanding the BIM/VDC workflows and Electrical constructability during the Pre-construction phase. Now, eight years after landing in America, he’s keen to help more WBE clients benefit from all that BIM and VDC offer.
What does the BIM Manager role involve?
Masnopita coordinates the construction model process and works with all the trades’ representatives to ensure that nothing clashes within the virtual model.
Once the model is complete (all items populated and coordinated), the BIM team provides the installation drawings to the field crews so that they’re all following the same model. The benefits are obvious.
Masnopita says that it’s almost impossible to foresee all the problems if your plans are only on paper.
“Previously the field guys were fighting for space to arrange everything in the same small space. Somehow they end up putting all the ductwork, plumbing pipes, mechanical piping, fire protection and electrical plus lighting and telecom into one small ceiling.”
It’s no wonder that tempers flare on occasion.
“All that is taken away in the BIM process. Everything is streamlined so the field guys can focus on what they’re supposed to do, which is installation.”
At the end of the build, Masnopita presents the owners with an as-built model which shows the building precisely as it has been constructed, right down to the position of card readers, security camera and lighting.
This model can inform maintenance and alteration decisions for years to come. Moreover, every time a change is made, the model can be updated to keep it current.

How do BIM and VDC improve the design and construction process?
BIM lets WBE clients see and understand what will happen on their build and monitor potential costs. Before anyone sets foot on the job site, each stakeholder can extract the information they need to order the exact amount of material needed, minimizing waste (and cost overruns.)
Then, once everyone has contributed to the designs and agrees on the schedule, the project moves to the construction phase with a clear timetable to follow.
Sometimes, despite all the care, a contractor may find something that the BIM process has missed. They have to go “old school” and make some changes on the spot. Once those changes are made in real-time, Masnopita and the BIM team adjust the simulation to produce an ‘as-built’ model, which shows the building exactly as it is in reality.
That’s incredibly useful for present and future facility management. Whenever any work or improvements need to be done, the owners and contractors can pull up the as-built models without further research.
Having a living 3D model is a vast improvement on poring over huge flat PDFs because 2D requires six different representations of the same room to cover all the angles. (Top, side, walls etc.) But when you navigate through the 3D model, you can manipulate the model to show all the different views at the same time.
Of course, the up-front costs of using BIM and VDC can be seen as expensive, and it does stretch the time needed during the design process. However, Masnopita points out that the immense savings more than balance those costs in time, money and materials during the actual build.
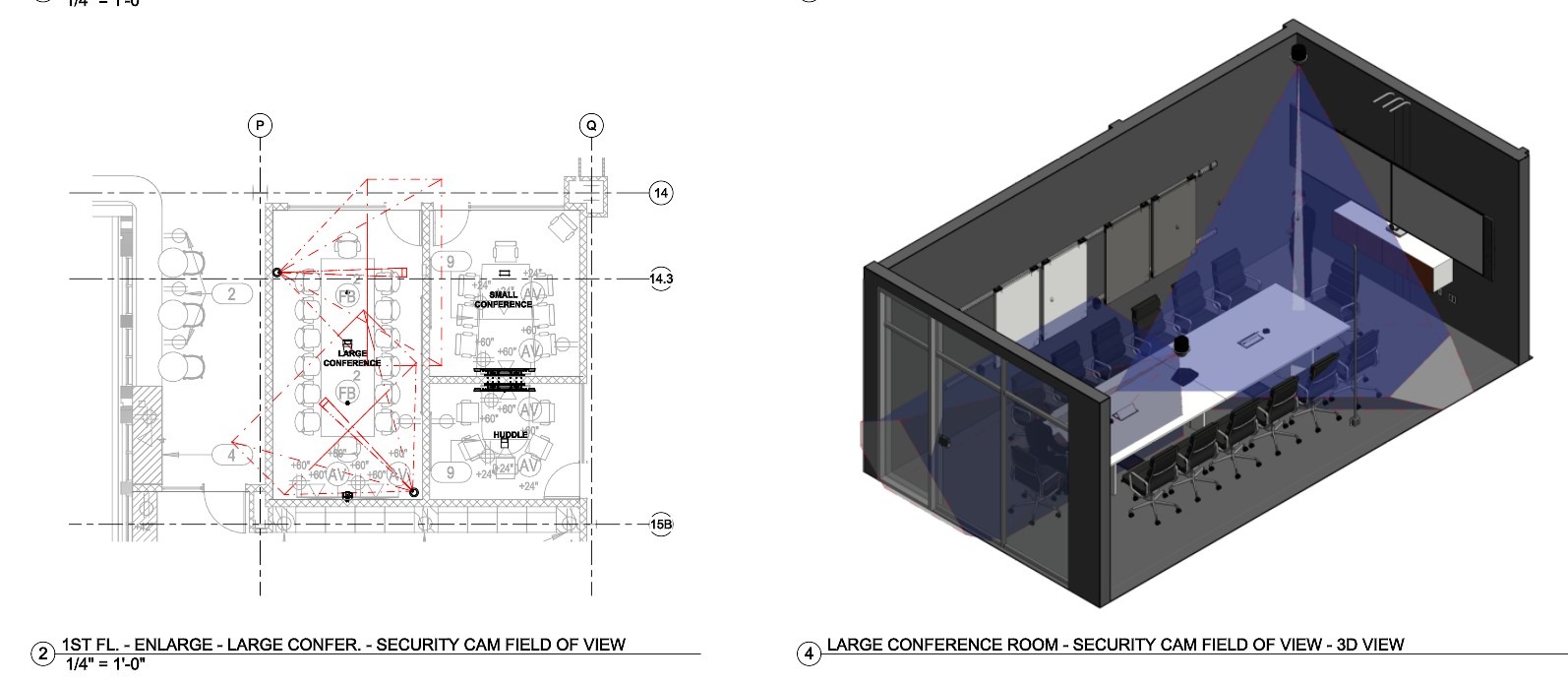
BIM Education
Another facet of Masnopita’s role with WBE is teaching the contractors and modelers how to work together using BIM to maximize its usefulness.He points out that while the modelers are computer software and tool experts, they frequently have no construction experience.
At the same time, the contractors have worked on construction sites all their lives. They know all the procedures on the ground but have little or no experience with tech.
His role is to get the two sides together, collaborating as a team so that the modelers can understand what does and doesn’t work in the real world. At the same time, the contractors can see how working with such a detailed virtual model can iron out problems before they happen.
Masnopita sees this education component as an investment in the present and future, saying that a few hours working together on one BIM project allows contractors and modelers to take their new learning onto future builds, too.
Masnopita has several possible ways to work with supervisors and their teams to show them the possibilities of BIM and VDC. Sometimes he’s able to bring them to WBE and demonstrate the model in person, showing how it can change and adjust with their input and answering their questions.
He can also work remotely with a team, using a screen share to demonstrate the building model. And occasionally, he takes his laptop into the field and gets the team together in the site office. He’s happy to accommodate any scenario that works best for the team involved.
An AV room walkthrough
VDC simulations allow designers to see how selected equipment will function before it’s bought and installed. Have you ever been in an important meeting and found that you couldn’t hear because you were in a microphone dead spot? Or come out with a headache thanks to poorly-placed speakers? Has your firm installed expensive security cameras and afterward discovered a blind spot?
Masnopita showed us how WBE’s AV division could use VDC to eliminate microphone, speaker, camera and lighting problems before purchasing or installing a single item.
“We don’t just model the items. We also show the field of view of a specific camera type. So if you place a camera in a room or outside of the building, you can arrange to see the view range of that camera. What is it covering? Should they switch to another camera over an area, or is that camera sufficient? We plug in a few numbers from the camera properties and see how much that camera covers before you buy or install it.
The same goes for the speakers or microphones inside of the room. You can identify if one speaker is enough in the ceiling or if you need two because you can show the coverage like a prism. How much of the room is it covering?
And if it’s not enough, you try adding a second one, or you can change to a different speaker with a bigger coverage. It helps to decide how many you need to buy and which brand will be the best in that situation. Then you input the microphone. If you have a table for 12 people, one mic will have to cover everything from each side. So you place two and show the coverage as a big bubble.”
Masnopita demonstrated how the model extends to the vital elements usually hidden behind walls.
“This is the mounting plate. When I measure it (virtually), it tells me we need a two-inch long screw to mount it. Then we show the conduits in the ceiling and the walls. And this is the box where the conduit goes to the receptacle, so you can see where to plug in your phone to charge. There’s the card reader at the entrance. Again, let’s check the product – and there is the electrical and material data and the manufacturer. That’s useful for when you need to replace or repair machinery. The model has all the specs right down to the serial numbers.”
Zooming around this model looks and feels like an enormous video game. That’s one of the things that attracted Masnopita to the technology in the first place. But it’s a “game” with vision and purpose.
With one quick simulation, you know precisely what to order and where to place it before the room has even been built. And with wait times for machinery sometimes extending for months, it’s a distinct advantage to have such certainty before placing the order.
Conclusion
It’s clear that BIM and VDC are the way of the future. Since bringing Masnopita on board, WBE is already using the technology with excellent results across many of its divisions.
“We have been providing the telcom and security systems design assistance on our 10x Genomics project,” says Masnopita, “by showing and modeling all the security cameras and card readers to enter the building. That included all the conduits that power those card readers outside of the building to be able to open the door and security cameras throughout.
The entire Power (equipment, conduits with supports and devices), Lighting (light fixtures, panels and sensors) and Telcom (cable tray, equipment and devices) system infrastructure were modeled and coordinated by us, before the field crew started installation by using our drawings produced from the model itself. We did all sorts of supporting site work, too, with light poles on a parking lot, Underground conduits, trenches for laying them – the lot!”
In time, it will become standard practice to use BIM and VDC on a building site, much as CAD is expected today. WBE is proud to offer design-assist, technological education and as-built models to help clients and contractors maximize efficiencies and create a streamlined design and build process across all their projects.
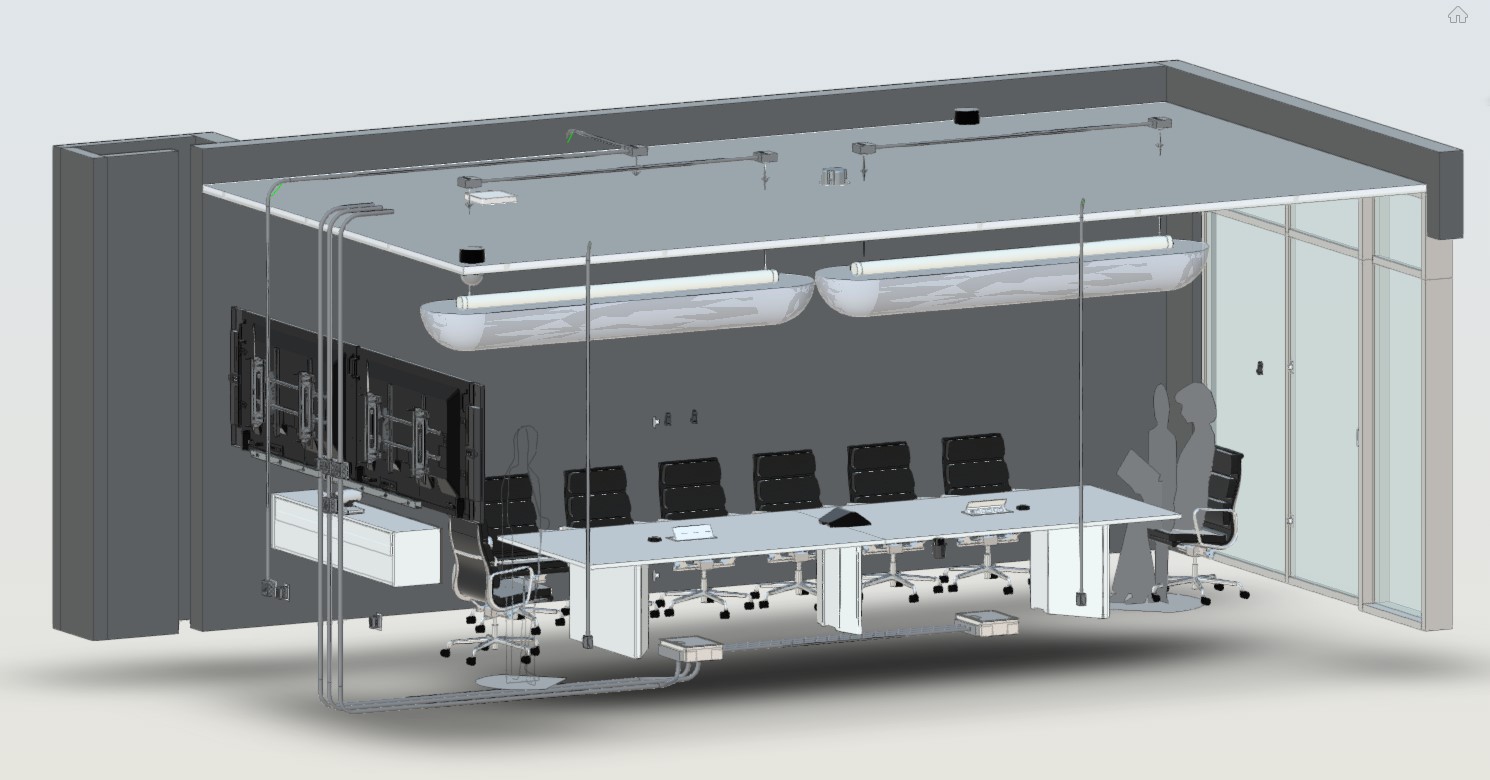